How AkzoNobel is optimising its supply chain
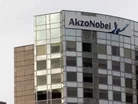
With 400 years of technical and product innovation behind it, global Fortune 500 company AkzoNobel is one of the leaders on the Dow Jones Sustainability Index. And, as with any successful organisation, it continuously looks to create tangible business value from its projects, and in particular increase productivity and growth.
One area of the business that wanted to improve its productivity was the Powder Coatings division, the products of which are used on everything from metal furniture and window frames, to radiators, pipes and cars. Seven of its factories in Western Europe were facing challenges with matching demand for its products with capacity. To solve this puzzle, the operations team needed to increase its capacity utilization and productivity, and ultimately improve customer satisfaction.
The business unit was facing the problem of very high inventory levels, sub-optimal utilization of plants, inconsistent service levels, a lack of supply chain visibility, and duplication of planning tasks across various plants. The seven factories had different scheduling systems in use and no integration; data from the plants were stored in separate locations with no easy way to access information or create synergy between the sites.
Consequently, it was difficult to handle all these complexities, even at a local level. Centrally, it was impossible to get efficient cross-plant visibility or optimize plant capacities.
This was when Pierre Versailles, Operations Excellence Manager, became responsible for implementing a new supply chain planning solution. AkzoNobel needed an approach that was flexible and could adapt quickly; for this reason it chose the Quintiq platform.
The new system went live in 2011, followed by the rollout – ahead of schedule – to the seven plants. “Quintiq’s configurable user components make it possible to have a certain level of customization while using single software architecture across all sites,” said Versailles. “This was a very important factor as it facilitated the fast rollout of the Quintiq platform to all seven sites.”
By using Quintiq’s platform, comprehensive and complex planning was made more efficient and effective. The quality of the planning process and delivery performance – in terms of accuracy and reliability – improved, which allowed managers to foresee every scenario and help them make better informed decisions.
Quintiq supplied trainers to help AkzoNobel’s planners get used to the new system. “Beyond the flexibility of the software, the Quintiq consultants provided us with practical advice, advanced mathematical solutions and challenged us all the time,” said Versailles. “This was key to the successful implementation of the Quintiq system.
"Full transparency was achieved through the combination of centralized strategic planning with decentralized tactical or operational planning in our seven plants. We are seeing positive results in terms of capacity compensation and improvements in planning. This in turn has led to a better customer service and optimal productivity."
The success seen since the go-live of the project has led other business units within AkzoNobel to review their scheduling systems. Three sites for its Decorative Paints business, covering 250 million litres of paint per year, is currently undergoing transformation.
The overall challenge was getting a high quality, fully automated schedule in place, allowing the three sites to hit optimization performance targets. However, with constraints on manufacturing including mobile, vessels and other tools, and complex cleaning rules, the business unit needed an agile and adaptable system; something the old system couldn’t deliver, but Quintiq could.
Pulling data from an ERP system that dealt with order processing, Quintiq’s software generates detailed schedules for all dispersing, mixing and filling operations across the manufacturing process. This increased productivity, shortened downtime and cleaning intervals, and reduced the company’s use of cleaning agents.
Stephen Walsh, former planning analyst at AkzoNobel, who will be speaking at the Gartner Supply Chain Executive Summit in London (19 – 20 September) on the project, said: "Quintiq has an impressive culture of problem solving and now AkzoNobel has a world-class scheduling tool which can be easily adapted to additional sites. The implementation was more complex than we had expected, but the results justify the effort.”
By Arthur Torsy, General Manager of EMEA and Latin America at Quintiq
Read the August 2016 issue of Business Review Europe magazine.
Follow @BizReviewEurope