Tech advances mean datacenters need more cooling – does yours?
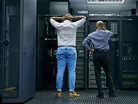
Datacentres are out of date. They are built to last but, let’s face it, technology changes fast. What’s under the hood in a datacentre today often far outpaces the capabilities of the structure built to house it. Modernisation is on the cards for data centres globally. For South African data centres, cooling is going to be a priority.
Increased use of technology and advances in technology mean more power, cooling and space are required in data centres. As demand continues to grow, data centres are being compelled to upgrade. In fact, IDC puts modernisation high on its list of 10 key predictions for the global data centre market. It forecasts that by 2020 the demands of next-generation apps and new IT architectures will force 55% of enterprises to upgrade their existing facilities or deploy new facilities. Does that hold true for datacentres in Africa and South Africa?
SA data centres get the basics right
Datacentres power businesses, serving up the connectivity and functionality needed to operate, communicate and transact. In South Africa, a number of new datacentres are now being built. Microsoft has, for example, recently announced that it will deliver cloud services from data centres in Johannesburg and Cape Town in 2018. The drivers are not just the fundamental growth in data and the criticality of always-on connectivity to function in a digital business environment, there are clear advantages to keeping data local—bandwidth is cheaper, the data is more secure in terms of where it is stored, and it’s still easier to meet local data security and privacy regulations than to jump through foreign hoops if data is stored or served up via international data centres. For both older data centres and the new centres in design and build phases, getting the basics right will be fundamental.
For a data centre two things are vital: power and cooling. If either of these elements fail, the data centre will fail. And today the cost of failure is high—for every business that has a server on a rack. Redundancy is key. Diesel generators can take care of power needs if the main feed goes down, but what about cooling capacity? In Africa, power outages remain a reality, energy costs are rising and temperatures can be extreme all year round. This impacts datacentre operations from a functional and cost perspective.
Advanced cooling for different applications
Data centres need lots of cooling fast and this usually means big chillers with high capacity outputs are required. These require considerable investment. They also come with 20-35 year lifespans, which is not always a good thing. Older cooling equipment requires a lot of power—and time—to start up and reach the right cooling outputs, putting a lot of pressure on power supplies, especially where there has been a power failure and generators are in use. More modern, advanced chillers, with features such as fast soft-start variable speed drives (VSDs), which easily and rapidly adapt outputs to meet changes in the environment while delivering optimised energy efficiencies, offer more benefits. This drives the case for upgrading and for ensuring that appropriate cooling solutions are part of the design.
What cooling equipment is implemented will depend where the data centre is situated and the rationale driving the acquisition of the cooling equipment. If, for example, energy efficiency is key, a solution like Johnson Controls’ YMC2 water cooled chiller—the most efficient VSD chiller on the market which takes only 20 seconds to get to full load capacity (rather than 20 minutes) — may be the answer. However, it may not be the most effective solution if the data centre is located in water-scarce Cape Town or elsewhere in Africa.
In these instances, an air-cooled chiller, like the YORK YVFA Air-Cooled Variable Speed Drive Screw Chiller may be more suitable. In addition to its VSD compressor, which lowers energy consumption, it has one independent refrigerant circuit per compressor, providing ultimate redundancy. So, even if a compressor fails, partial cooling capacity can be maintained via the second or third circuit. Another advance worth considering in this chiller is its energy-optimised hybrid cooling mode and air-to-liquid free cooling coils. These are intelligently controlled to maximise efficiency year-round, automatically. In fact, Johnson Controls is the first manufacturer to utilise free-cooling coils that are integrated within the chiller.
For precision air conditioning in data centres, custom close control air conditioners like the YORK YC-P range of close control units (CCUs) are useful. IDC predicts that by 2021, the expanded use of power-hungry accelerated computing technologies will have forced most major data centre operators to adopt a modular approach to deploying power/cooling assets in their facilities.
Unlike comfort air conditioning, close control systems operate constantly 24/7, so they need to be high on reliability and low on power consumption. Since no two critical cooling requirements are the same, custom CCUs make good sense. They usually come in a variety of models, from 20kW to 150kW range and are available as either direct expansion or free cooling models and EC variable speed motors for energy efficiency. The added value of these units is that they can integrate with a building management system (BMS) an increasingly vital component for controlling the data centre environment.
Improved controls
A BMS dashboard can be customised to constantly report on key indicators of the health of the centre, such as the status of the power supply, the charge left in batteries, fuel status of generators and the temperature in the data centre. With constant monitoring and alerts, the data centre’s risk is lowered and controls are increasingly automated.
As data centres continue to expand their client bases in South Africa, ensuring that the fundamentals – power and cooling – are in place means exploring new chiller technology in the planning and design phase to ensure benefits, and doing the math and taking action on modernisation of more established centres.
Neil Cameron is the General Manager of Building Efficiency at Johnson Controls Area – Africa.
- DHL Forwarding: invests US$8.29mn in South Africa facilityLeadership & Strategy
- Blue Chip: Fundamental to Wesleyan’s data centre migrationTechnology
- Trialogue: CSI spend hits R10.7 billion in South AfricaLeadership & Strategy
- Emirates signs agreement with Airlink expanding reach in SALeadership & Strategy