Google Cloud: UK manufacturing, operating in the new normal
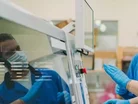
The UK manufacturing industry has shown the first signs of recovery since the initial disruption caused by Covid-19, after a survey showed that factory output had declined at a slower pace in May than it had in April.
The monthly industry snapshot from IHS Markit and the Chartered Institute of Procurement and Supply indicated that the downturn in the manufacturing sector eased last month due to lockdown measures gradually being lifted. Prior to this, the impact of the Covid-19 pandemic and the steps taken to mitigate the spread of the disease caused the steepest decline in output, new orders and employment in the survey’s history. Public lockdowns, company shutdowns and social distancing measures all presented significant challenges for the industry.
Pockets of growth were seen as manufacturers who traditionally haven’t served the medical industry responded directly to the increasing pressure on the health system and associated shortage of critical care equipment such as ventilators and personal protective equipment (PPE). And in certain circumstances, consumer and commercial electronics device manufacturers were able to provide key components from their inventory to medical device manufacturers.
Despite the first signs of recovery being positive, the industry still faces a number of challenges that may take longer to solve than first expected. As manufacturing companies plan for the longer term, it will be critical for them to adapt in a way that both strengthens operations and builds business resilience.
Accelerating digital transformation in a changed world
Digital transformation is a concept that has been around for years. Whilst manufacturers have been utilising automation and robotics for a long time, following Covid-19, the industry acknowledges the need to fine tune a long-term digital roadmap to improve foresight and agility, especially when it’s been difficult to predict demand and supply.
It’s no longer enough to rely solely on historical data. Enterprises must put their data to work at very high granularity to improve foresight into different factors that affect both demand and supply. These companies should leverage a combination of both internal data and external influencing variables to improve forecast accuracy and inventory turns, all to optimise their operations in real-time.
Artificial Intelligence (AI) – and utilising data – is central to this solution. Manufacturing benefits from experiential learning that uses knowledge to automate processes. By recording what works or doesn’t work, manufacturers can easily use a digital-first approach. Additionally, AI can optimise manufacturing by applying knowledge from automated processes, or from interpreting huge datasets. By removing the guesswork and predicting disruptions from externally sourced data, (such as weather, traffic, transportation cost, and competitive and raw material pricing), AI can help operational teams make informed decisions.
The new paradigm that the manufacturing industry needs to adapt to has brought into plainsight the importance of digital technologies and platforms to stay operational. But it’s no longer only data insights that manufacturers gain from digitalising and adopting emerging technologies. Health and safety, communication and collaboration, minimising human touch, and ensuring business continuity have become critical considerations, too.
In the short-term, another consideration is how to keep businesses running in an environment of reduced worker capacity and increased worker safety requirements. Some companies, such as Google Cloud, are developing easy-to-use solutions based on interoperability, analytics and machine vision, which is an engineering-based system using existing technologies to mechanically 'see' steps along a production line. These solutions help customers to remotely monitor and manage their operational technology, mitigate risk of health-related absenteeism, ensure worker safety and reduce the amount of manual labor needs in a factory, particularly for quality control processes and procedures.Manufacturers can also further leverage these AI-based tools to enhance worker capabilities and drive greater optimisation both now and in the longer-term.
Driving smarter productivity in new ways of working
The industry’s “recovery mode” will rely heavily on how well it overcomes the challenge of operating efficiently with social distancing measures in place and without any certainty around how long public health measures will continue. Now more than ever, it’s essential that manufacturing organisations provide employees with the right tools to foster collaboration amongst a distributed workforce, particularly when there may be skeleton crews at factories and more people working from home.
Organisations also need to consider communication and collaboration between different time zones, ensuring that employees can easily and quickly access company files and participate in virtual team meetings. Employees need to effectively communicate – whether that’s through a live stream for the whole workforce, supporting an interactive team meeting for a department or facilitating urgent one-to-one or team communications. Most importantly, it’s not only about having the foundation to manage, but it’s about using technology that will drive smarter productivity.
The ‘new normal’ will be one of the toughest recovery environments many manufacturers will ever have to face, lined with changes to working environments, uncertainty about how long the pandemic will continue for or what demand will look like in the next recession. While a number of challenges threaten to derail the industry’s rebound, leveraging data intelligence, advancing technologies and the industry’s learned experience from Covid-19 will give the manufacturing sector the best chance of overcoming the barriers that lie ahead.
For more information on business topics in Europe, Middle East and Africa please take a look at the latest edition of Business Chief EMEA.
- How analogous inspiration can solve your strategic deadlockLeadership & Strategy
- Cloud is driving IT spending through the roof across EuropeTechnology
- Companies are realising a rapid return on AI investmentsTechnology
- Siemens and Microsoft: Driving cross-industry AI adoptionDigital Strategy