Article
Digital Strategy
Lean Six Sigma success secrets
By Bizclik Editor
May 19, 2020
undefined mins
Share
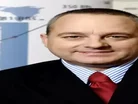
1. READYING THE ORGANISATION
2. DEPLOYMENT STRUCTURE & PROJECT SELECTION
3. KNOWLEDGE TRANSFER, BELT COACHING & PROJECT REVIEWS
4. DEPLOYMENT & PROJECT TRACKING
5. REPLICATION & MAINTAINING MOMENTUM
Share
Featured Articles
SAP has announced it has appointed a new President for a newly-created EMEA region, aiming to make the most of the opportunities of cloud and AI technology
Technology giant SAP has expanded its portfolio with the acquisition of LeanIX, a leader in enterprise architecture management (EAM) software
To help businesses achieve increased productivity, Siemens and Microsoft are deepening their partnership by showcasing the benefits of generative AI